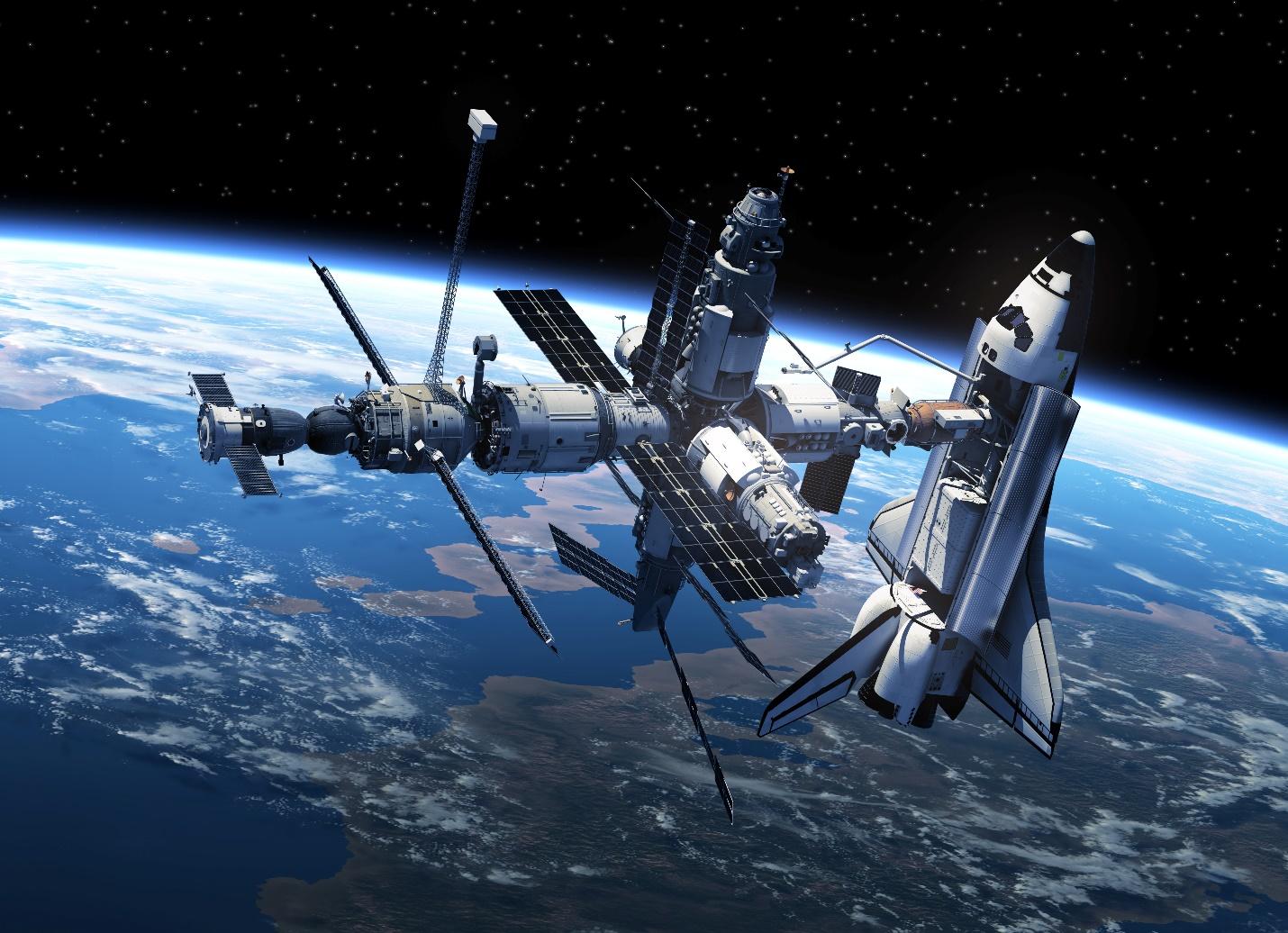
As a $116 billion industry in the U.S., scrap recycling is responsible for disposing of roughly 260 million tons of waste each year. With that kind of responsibility, more and more recycling companies are looking to advanced technology to improve operations, and there have been some notable innovations in recent years.
And one of them is truly out of this world.
As part of the ongoing push to find ways of improving the processes and techniques of scrap recycling, university researchers and private sector companies have been developing sophisticated new technologies for making old metal into new steel and aluminum.
And one of the latest technological innovations comes courtesy of a major federal agency, NASA, with their new creation being used at the International Space Station.
The device, dubbed the Refabricator, is designed to take a truly creative approach to recycling: it recycles old tools so they can be used to create new tools – in space.
For the scrap metal recycling industry, it’s a reminder that the technology behind recycling can boldly go into new and exciting directions.
And it’s also possible that news about the International Space Station using recycling could help spark renewed interest in recycling back home. If recycling older parts on the space station can reduce operations and maintenance costs – it’s worth noting that the same concept applies to scrap metal recycling in general. Using recycled scrap metal to make new products helps hold down the expenses that manufacturers incur – and those savings can be passed on to consumers.
And that’s only one of numerous strong arguments for why we need to boost recycling rates both nationally – and globally.
How is NASA Using Recycling to Reduce Costs?
As stated, the latest technological innovation to become a part of the operations of the International Space Station is a 3D printer, which is being sent to the orbital laboratory aboard a Northrop Grumman spacecraft.
Northrop Grumman delivers a lot of supplies to the space station (up to 7,400 pounds at a time) to aid in investigations and research projects conducted there. But it can be very expensive to get those supplies delivered.
That’s where NASA’s new 3D printer and recycler, called the Refabricator, comes in. It’s the first of its kind used on the space station, built specifically to take materials, such as old 3D-printed parts, and recycle them.
The Refabricator’s capabilities include turning waste materials and 3D printed parts into high-quality 3D printer filament, which can be used to create new materials. The plan is to use the materials multiple times to create parts. This reduces the need to ship new supplies to the space station and therefore saves money.
NASA noted that this project was launched for that reason: to reduce the cost of resupplying the space station. This technology is also expected to prove beneficial for future exploration missions to the Moon and Mars.
NASA noted in a news release that the 3D-printer technology is expected to, “greatly reduce the need to continually launch large supplies of new material and parts for repairs and maintenance.” Built by Tethers Unlimited Inc. of Seattle, the Refabricator first went through flight certification testing at NASA’s Marshall Space Flight Center in Huntsville, Alabama. Its operations will be controlled remotely from Marshall’s Payload Operations Integration Center.
The Refabricator is unique as the first-ever integrated recycler-manufacturer in orbit, and there is a hope for a long-term and expansive use of recycled metals and plastics being made for new parts. Although this machine is only about the size of a mini fridge, it provides a significant boost to in-space manufacturing by reducing the need for parts to be rocketed into space when something breaks on the International Space Station.
Sending replacement parts or tools for everything used on the spacecraft, and resupplying these parts from Earth, is extremely costly and that takes far too long to complete. The Refabricator could become a highly successful model to fabricate, recycle, and reuse parts and waste materials.
It’s a fascinating concept: recycling in space. But at the same time, the logic behind it is similar to one of the top reasons why we push to increase recycling rates on Earth as well.
Why Should We Work to Boost Recycling Rates?
Scrap metal is far too often written off as junk, something that needs to be disposed of, which is why so much scrap ends up in landfills.
Environmentalists have been warning for years that this is a mistake, since scrap contains toxins like mercury and lead, which can contaminate the soil and water around our landfills. That poses significant health risks to both people living nearby and wildlife.
The environmental benefits of recycling scrap metal, on the other hand, are well documented. Scrap can be successfully recycled to make new metals, which can then be sold to manufacturers to create new products. And that removes scrap from our landfills.
In addition, recycling scrap metal for resale eliminates the need for manufacturers to rely on mining for virgin ore to create brand new raw metals. With recycling, we’re not using up our natural resources as we would be through mining.
But there are also considerable economic benefits to recycling.
As we discussed, the Refabricator was created to cut down on the need to constantly ship replacement parts and materials to the International Space Station. In a similar way, recycling scrap enables our nation’s manufacturers to reuse metals and precious resources. Most metals can be recycled over and over again, offering consistent value. There are a lot of savings to be had when we turn to experienced recycling firms like GLE Scrap Metal to provide manufacturers with metals needed to construct everything from autos to home appliances and furniture.
Recycling scrap metal saves money by reducing the cost of production during manufacturing, while also eliminating the need to mine or manufacture new raw materials. Lower manufacturing costs can help keep prices down.
There are other economic benefits. As the National Institute of Health notes, recycling metal creates six times more jobs than sending the metal to a landfill. The National Recycling Coalition has noted that the recycling industry, in general, generates $236 billion annually, and the scrap metal recycling industry employs more than 400,000 people across the country.
As NASA has discovered, the way to cut down on the need to replace important supplies is to reuse what you already have. The Refabricator provides a way to recycle in space.
If that can be accomplished, then we can definitely find ways to get more consumers, businesses, organizations and municipal governments to do the same here on Earth.
Conclusion
The scrap metal recycling industry is expected to grow in the next few years as the global economy gets stronger. Consumer demand for cars and other products is ramping up the manufacturing process, and using recycled metals helps reduce the cost of making those products.
It’s a lesson NASA has learned as they bring recycling technology to the International Space Station: you can save valuable time, money and resources by recycling.
What we need now back on Earth is to educate consumers and businesses about the need to increase scrap recycling rates.
Individuals and businesses can bring their scrap to GLE Scrap Metal, a premier scrap metal and electronics recycler that performs environmentally friendly processing and recycling of all base and precious metals.
To learn more, contact GLE Scrap Metal today at 855-SCRAP-88 to request a quote.