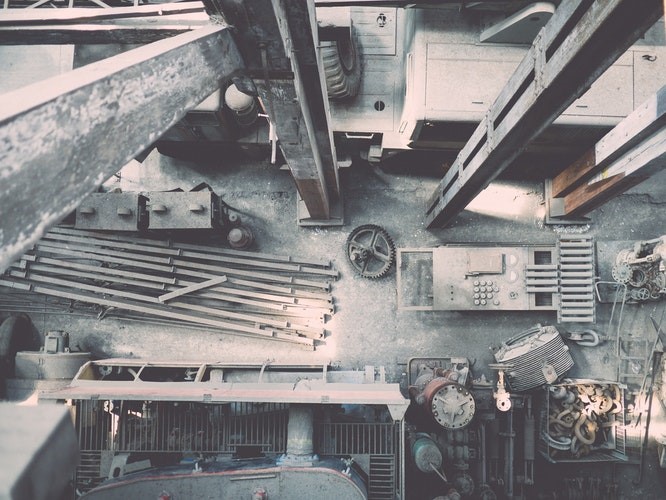
“Reduce, Reuse, Recycle.” As children, we hear this phrase often. But, what does it really mean, especially when it comes to the process of metal recycling?
With metal recycling, these 3 things work together to protect the environment. When you recycle your scrap metal, you create a way to reuse the metal and reduce the need to mine and produce more.
So, what exactly happens to scrap when it does get recycled? Good question. In this article, you will discover the step-by-step process of how metal is recycled – from start to finish.
To begin, we need to go over what you should do before dropping your scraps off at a metal recycling facility.
Your Part: Preparation
If you have a lot of scrap metal accumulating in your home or business, don’t dispose of it in the trash. Instead, send it to a trusted metal recycling facility.
But, before you send them off, we recommend separating your metals. First, separate them by ferrous and nonferrous metals. To help, you can use a magnet and wave it over your scraps. Ferrous metals will stick to the magnet because they have iron.
Then separate your metals by type. For instance, you will want to separate your copper, aluminum, steel, and so on into different bins. Any sorting you do will help the value and get you a greater return, as well as help out the facility.
If your business is setting up a metal recycling plan we recommend performing a scrap metal audit to help you maximize your returns.
This brings us to the actual process of metal recycling.
How Is Metal Recycled?
For starters, the process that metal goes through is a circle. It starts with a consumer using a product made out of metal and ends with another consumer using a new product made out of the same metal.
In between is where recycling facilities come in. We recycle the metal so manufacturers can reuse them.
Keep reading to learn our 7 steps to metal recycling.
1. Collection
The first step of the collection process starts with you. Whether it is at your business or home, scrap metal is all around you.
Designate bins in your garage or facility specifically for collecting your scrap. Make sure the bins you use can safely hold the metal.
If your business has a lot of scrap metal, some recycling facilities may help you arrange transportation.
2. Sorting
Once the facility collects the scrap metal from you, they will begin the sorting process. Although the collection may have been previously sorted by the donator, this is done for quality assurance.
First, metals are separated from other materials. Plastic is stripped from wires and metal pieces are removed from items. Then, with the use of magnets, ferrous metals and non-ferrous metals are separated.
Sort By Type and Cleanliness
After that, the metals are sorted by type. This is done by looking at the color and weight of the metals. For example, copper is yellowish-red while aluminum is silver.
Finally, metals are separated by cleanliness. This means if the metal is pure or impure. An automated operation includes magnets and sensors such as infra-red scanning and x-ray.
3. Processing
This brings us to our next step, scrap metal processing. During this process, the metals are first compacted and squeezed together to take up less space. Then, they are cut into smaller pieces with hydraulic machinery.
The hydraulic machinery is able to produce enough pressure to cut large pieces of metal. This is because it uses a fluid that flows through motors and throughout the machine to pressurize it.
Next, it is shredded into even smaller pieces by passing it through hammer mills. Shredding the metal makes the melting process easier because, when the pieces are smaller, it creates a larger surface-to-volume ratio.
4. Melting
With a large furnace, the metal is now melted. The furnace is set for each particular metal because each requires different levels of heat. This is because different metals are made out of different properties.
The size of the metal and the furnace will impact how long it will take to melt. It can be anywhere from minutes to hours. While this process does involve using energy, it is far less than needed to mine new metals.
5. Purification
To ensure quality, the metals are purified from any contaminants.
One method of purification is electrolysis. In this process, an electric current is passed through the metal and the pure metal is deposited at the cathode while the impure ones are dissolved.
The impure metal is an anode and the pure metal is a cathode. The soluble salt from the metal is an electrolyte. These impurities collect below the anode, also known as anode mud.
On the other hand, other metals just need to be passed under a strong magnet that can separate the metals.
6. Solidifying
This is the final process the metal goes through before being sent out. First, chemicals are added to the melted metal to create desired properties.
The melted metals are then put through a conveyor belt that takes them to a cooling chamber to solidify them.
Some metals are melted into sheets while others into compacted blocks in a process called baling. This is done to make the production of new products easier for manufacturers.
7. Transportation
Now that the metals are purified and solidified, it is time to send out the metal to manufacturing facilities. The solid metals are packaged and transported on trucks.
Manufacturers are able to then make brand new products out of these metals. The products are then sold to consumers and then the process starts all over.
Why More Metal Recycling is Needed
Virtually every kind of metal can be recycled. Still, the current metal recycling rate of 30% is far too low.
Both businesses and people can benefit from recycling their scrap metal.
Financial Benefits
There is a clear financial incentive to recycle metal. Scrappers who collect scrap metals and bring them to a recycling firm can earn money for the metals they find. The same is true for businesses that collect their scrap and deliver it to a recycling firm like GLE Scrap Metal.
In addition, recycling holds down expenses in the manufacturing process. It costs far less to use recycled metals than to manufacture new products using virgin raw materials.
On top of saving money, recycling metal also allows manufacturing businesses to reduce their overall production costs. This then passes those savings on to consumers.
Another great way it benefits the economy is by creating a need for new jobs.
Environmental Benefits
Of course, there’s an important environmental impact of recycling metals. Recycling metals allow us to preserve natural resources.
It also uses far less energy to process than mining for virgin ore to get new metals. Additionally, it emits far less carbon dioxide and other harmful gasses. There are substantial energy savings from recycling scrap metal.
Another reason to not dispose of metals improperly is that you don’t want scrap to end up in landfills. These metals contain toxic chemicals like mercury that can pose risks to the soil and water near the landfill.
This raises the possibility that this carelessly thrown away scrap will potentially create significant health problems for people and wildlife in the area.
Recycle Your Scrap Metal With GLE Scrap
We all need to play a part in increasing recycling rates for scrap metal since it’s good for our environment and helps our economy as well. A great place to start is by taking your scrap to GLE Scrap Metal, a premier scrap metal recycler.
GLE will purchase, process, and re-integrate all recyclable metals while using environmentally-friendly processes.
Visit our website to request a free quote or call GLE Scrap Metal today at 855-SCRAP-88.