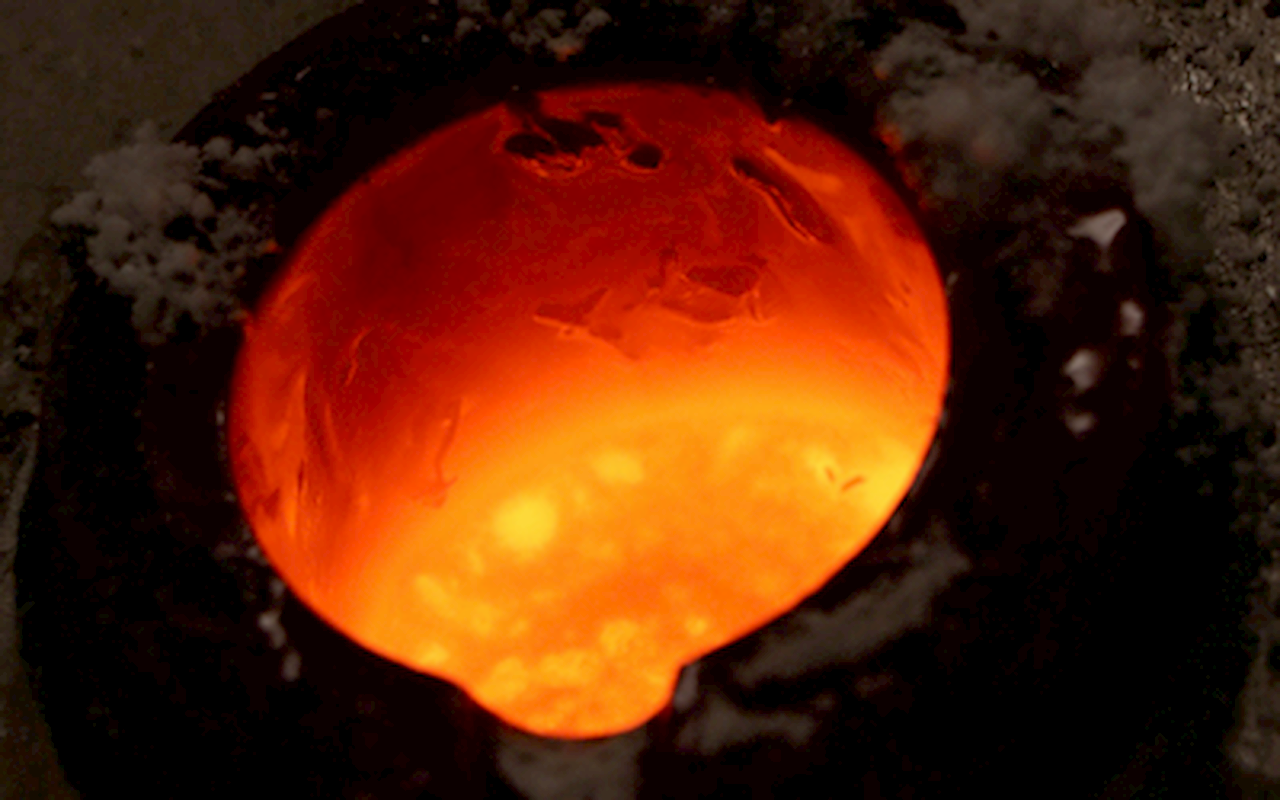
International trade and business have slowed to a crawl as countries everywhere deal with the strain of not having access to the raw materials needed to make most goods.
When companies can’t gain access to new resources, how can they maintain manufacturing?
Green steel may be one of the best ways for countries and businesses to secure the materials they need to keep the doors open.
What Is Green Steel?
Green steel is steel generated through new and improved methods of refining that create less pollution and carbon emissions than traditional blast furnaces. These methods include modern Electric Arc Furnaces (EAF), Molten Oxide Electrolysis (MOE), and Hydrogen Direct Reduction (HDR). The technology can also boast the ability to be cheaper to produce on average than traditional blast furnace methods.
Why Is Green Steel Important?
Green Steel historically has been a more expensive alternative to traditional steel making. In the last twenty years or so, methods have improved to the point where that’s no longer an issue.
So why haven’t steel makers switched over to New Technology?
Unfortunately, not every steel manufacturer has access to the same fuel sources, and there are staggering costs associated with renovating facilities in order to install this technology. Combined with the inability of the facility to produce steel while under renovation, it’s nearly impossible for most steel manufacturers to switch.
Instead, new steel manufacturers have come onto the scene with these improved technologies, cheaper and more efficient than their competition.
When Mining Stops, So Does Traditional Steel
The Coronavirus epidemic has broadly put a hold on traditional steel reaching the hands of manufacturers using blast furnace plants. This has caused a shortage of steel across the US and abroad as manufacturers turn to find new suppliers of raw and recycled steel.
How Manufacturers Make Steel
Depending on the method used to create steel for manufacturers to produce goods like cans, rebar, and structural steel, changes how they were affected by the pandemic.
How Blast Furnaces Work
Traditional blast furnaces use coal, limestone, and raw iron ore. They then create sinter and coke. Sinter is a form of iron that can survive in a blast furnace, and coke is a treated form of coal for the blast furnace.
The entire process requires more steps and specialized fuel sources than any other method:
- Coal
- Raw Iron Ore
- Coke Ovens
- Sintering Plants
- Blast Furnaces
- And Oxygen Furnaces
Because this method relies entirely on international supply lines to remain running continually, it puts Fabricators and Product Manufacturers vulnerable to pandemics, war, and trade wars.
Molten Oxide Electrolysis (MOE)
A relatively new method of smelting, MOE, only requires raw iron ore and electricity to produce steel. Not only does the process not produce oxygen, but it instead creates a fraction of the pollution generated from a blast furnace.
Unfortunately, MOE plants are still wholly reliant on raw iron ore– these high-tech furnaces can’t reach the temperatures required for recycled steel. Where MOE plants can reach temperatures over 1,500℃, EAF facilities can reach temperatures as hot as 1,800℃.
That’s half as hot as the surface of the sun.
Electric Arc Furnaces (EAF)
Electric Arc Furnaces are the best of both worlds between MOE and blast furnaces. EAF plants burn hotter than either of the other methods.
They also use electricity instead of coal like MOE, but burns hot enough that they can use both scrap metal and iron ore to produce steel suitable for product manufacturers.
Why Haven’t We Always Used Arc Furnaces?
Arc Furnaces have been around since the 1800s. The problem has been the historically immense cost of electricity, and the need for something called Graphite Electrodes.
It’s only been with recent advances that electricity has been cheaper than coal for making steel. Meanwhile, there are only a few producers of graphite electrodes worldwide, with even less within the US.
Since the price and availability to use EAF is more available, producers are one of the most reliable sources of metal available.
How Coronavirus changed the game
Manufacturers and the public at large generally haven’t had to worry about supply shortages in decades. It hasn’t been a concern for so long that the majority of product manufacturers didn’t have a plan in place when the pandemic hit Europe and the US.
Now, after many years of complacency, companies are hellbent on having a proper backup plan in the future, while others have gone out of business competing for prices.
The Solution? Recycled Metal
Not just steel, but when shortages are high, the recycled metal needs to be widely available.
Sadly, not enough metal is being recycled. Most businesses today can benefit from contributing back with their scrap metal and trading back what they can with recycling centers.
Overall, recycled metal is:
- A cheaper, more reliable metal
- Creates less air pollution
- And recycled scrap benefits businesses, recyclers, and manufacturers.
How You Can Help Yourself
GLE Scrap Metal is a National Scrap Recycler with locations in Michigan and Florida. We can help your business with industrial, municipal, and commercial scrap. If you need help arranging a commercial pick up, or just looking to create a recycling plan to save your business money and fight pollution, give GLE a call.
We’ll help you create a comprehensive scrap recycling plan for your business. If you’re looking to help but don’t own a business, see our locations for residential recycling and help provide relief to the virus and pollution.