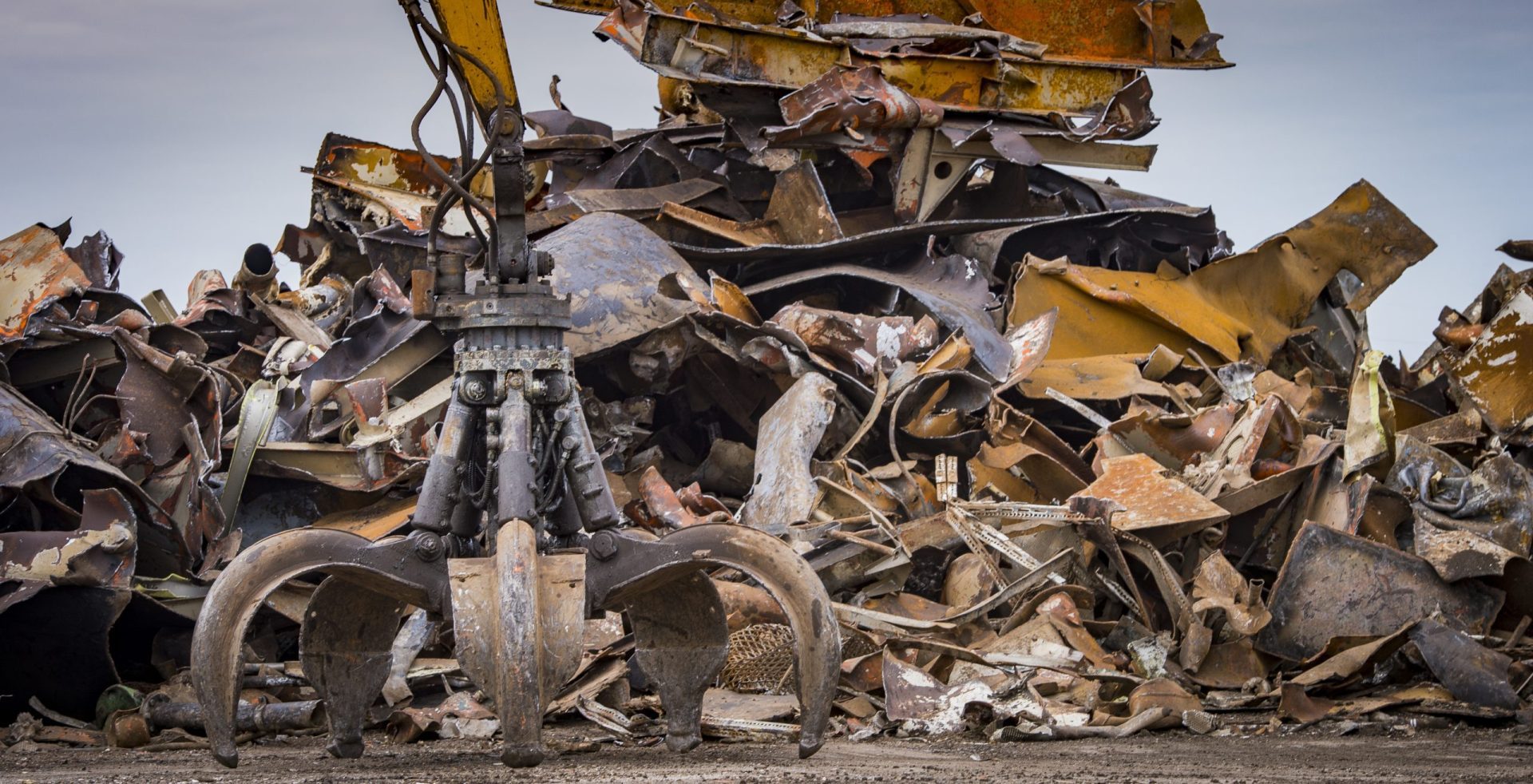
TL;DR
- Recycling can reduce the negative impact on our environment, and today, the recycling industry is not only expanding but evolving.
- Recycling companies are a $116 billion industry in the U.S. These companies are responsible for disposing of roughly 260 million tons of waste each year.
- Recycling companies are constantly investing in ways of improving their processes and techniques.
- Laser methods for automatic scrap metal sorting hold out the potential to offer huge savings at recycling plants.
- High tech solutions hold out the potential to make recycling a far less expensive and more efficient process.
- There continues to be a strong need for more consumers and businesses to recycle their scrap metal.
- Bring your used scrap to an experienced recycler like GLE Scrap Metal.
In our modern world, it’s simply not avoidable that we’re going to generate a sizeable amount of trash each week. This is a situation that continues to concern environmental groups who track the problems that waste creates for our environment. That’s why organizations are promoting recycling as an effective and efficient way to deal with the rising amount of waste.
Worldwide, consumers are generating more waste than ever before. Fortunately, recycling can reduce the negative impact on our environment, and today, the recycling industry is not only expanding but evolving. That’s due to investments and innovations within the fast-growing waste and recycling industry.
Recycling companies are a $116 billion industry in the U.S. These companies are responsible for disposing of roughly 260 million tons of waste each year. This amounts to 4.4 pounds of waste for every American on a daily basis. With that kind of volume, recycling companies are looking to advanced technology to improve operations.
This is particularly true for scrap metal recycling. This is a sustainable industry that’s promoting economic growth while helping to preserve the environment and our natural resources.
How Is the Scrap Metal Recycling Industry Evolving?
Recycling companies are constantly investing in ways of improving their processes and techniques. Today, scrap recycling centers are getting assistance from university researchers and sophisticated new technologies. It’s become a high-tech journey to make recycled scrap metal into new steel and aluminum. This saves manufacturers time and money because they don’t need to mine for iron ore. Scrap recycling has been taken to a new level of processing, where it can be automatically sorted.
Global Scrap Metal Recycling
In Japan, automobile recycling is mandatory, and scrap car parts typically get lumped together for iron. As a result, specific alloy elements in scrap don’t always get recycled in the most beneficial way.
A study was then conducted at Tohoku University. Researchers discovered that sorting scrap car parts into eight classes would increase recycling rates of alloy to more than 97 percent. This would save Japanese steelmakers, and their scrap metal recycling market, the equivalent of $287 million on raw materials. This also cuts down on greenhouse gas emissions.
The researchers studied the composition of scrap car parts and looked at what they could be used for. And they found that these types of recycled metals were best suited for nine steel alloys. They developed a process to have scrap metal melted down in electric arc furnaces and remade into steel products. During this process, the recycled alloy elements could be separated and also used. That’s expected to allow Japanese steelmakers to save up to 15.2 percent of what they spend on alloys.
The authors of this study noted that their methodology could be applied globally and to other industries. Their concept also helps promote the notion of a “circular economy.” This is where recycling allows scrap metal products to have a continuous lifespan. This also minimizes the likelihood of harmful environmental impacts from discarded scrap.
The authors of the study are also pushing for the development of new automatic sorting technologies for recyclers.
In Norway, Tomra Systems, a multinational corporation in the field of instrumentation for recycling solutions, developed a technology called laser object detection. Also known as LOD, this is meant to complement its existing automated scrap sorting systems. This was so that it can deliver higher quality scrap feeds.
This new LOD uses a laser scan across the ferrous metals and nonferrous metal scrap-carrying conveyor belt. It then identifies any non-metallics such as wood, rubber tubes, or glass. Once identified, they can be removed from the metals stream. That helps deliver a cleaner scrap product and ensures that anything unwanted in the scrap mix stays out. LOD is also expected to boost the recycling of large volumes of electronic scrap. This is because it helps separate wire and circuit boards from black plastics, ultimately adding value to the sorted scrap products.
The LOD innovation is expected to have a strong value in the United States market. Recently tariffs were applied on steel and aluminum imports to the U.S. by President Trump. Because of this there will likely be increased domestic production and increased consumption of domestic scrap.
In Finland, Kuusakoski Recycling has developed a new way to extract copper, titanium, and niobium from any hospital magnetic resonance imaging (MRI) scanners that have reached the end of their useful life. When that happens, there’s usually a variety of metals in the scanners that can be recycled. This includes copper and titanium-niobium superconducting wires used to generate the magnetic field that MRI equipment needs to function.
In the past, the superconducting coil that forms the core of MRI scanners was cooled with helium and scanner components were removed. In Kuusakoski’s new approach, just the outermost structures of the superconducting coil is dismantled with flame cutting, rather than the entire coil. This process helps separate the coil’s copper wire for reuse.
In Austria, Redwave has a Compact Redwave XRF/C technology. This technology can reduce scrap costs by using X-ray fluorescence sorting technology. The x-ray detects the elemental composition of mixed metals passing through it. Materials can then get separated into two streams that are collected by conveyor. Once there they’re separated further, with automated sorting putting them into different metal fractions. This technology also uses advanced software algorithms to differentiate between desirable and undesirable elements.
What Advantages Do These New Methods Hold?
Laser methods for automatic scrap metal sorting hold out the potential to offer huge savings at recycling plants. But, in the long run, it also holds out the potential for large economic savings as well. Identifying each metal component in scrap can help ensure that every part can be sorted and recycled. This means more metals available to make new products. That helps hold down the costs of making new products.
There are also clear environmental benefits. More than 132 million tons of municipal solid waste gets discarded in landfills each year. However, that is just, at maximum, 35 percent of nonferrous and ferrous scrap that is recycled.
The scrap that ends up in landfills poses serious environmental risks to the soil, air, and water. This is due to the toxins contained within them, like mercury and lead. That’s a significant health risk if recycling rates don’t increase.
Not surprisingly, in the U.S. and across the country, governments are looking for innovative ways to recycle all forms of waste.
In addition to innovations in the recycling process, some researchers are also trying to improve the process by understanding consumers better. For example, researchers at WeRecycle, are studying how human behavior influences recycling rates. They’re installing GPS readers on trash cans that send signals conveying how many bottles have been thrown in that can. That data gets wired to a website so the recycling rates at each can will get studied. The goal is to determine where recycle bins should be placed to help maximize recycling rates.
WeRecycle has also developed an Android app that helps people find the nearest trash and recycling bins. Even at major outdoor events and parades! As the researchers noted, human behavior plays a key role in recycling.
Still, other companies are developing different approaches to recycling, including converting waste into biofuels through gasification technology. These companies are chemically recycling carbon molecules from waste to create products and transportation fuels.
High tech solutions hold out the potential to make recycling a far less expensive and more efficient process. It is a more appealing alternative to allowing scrap or used electronics to end up in the regular household trash stream.
Conclusion
Today, researchers and companies are looking for innovative ways to make separating metals more efficient, effective, and less costly. Those innovations hold out the possibility of significantly boosting recycling rates, which is a major contribution to our environment.
In the meantime, we all still have a role to play. There continues to be a strong need for more consumers and businesses to recycle their scrap metal. Bring your used scrap to an experienced recycler like GLE Scrap Metal. They perform environmentally-friendly processing and recycling of all base and precious metals.
This family-owned and operated business will purchase, process, and re-integrate all recyclable base metals. Which will then be supplied to domestic mills and global end-users to be transformed into new products.
GLE Scrap Metal also maintains a zero-landfill policy for scrap metals brought to use for recycling to utilize natural resources and help conserve energy.
To learn more, call GLE Scrap Metal at 855-SCRAP-88 and request a quote.