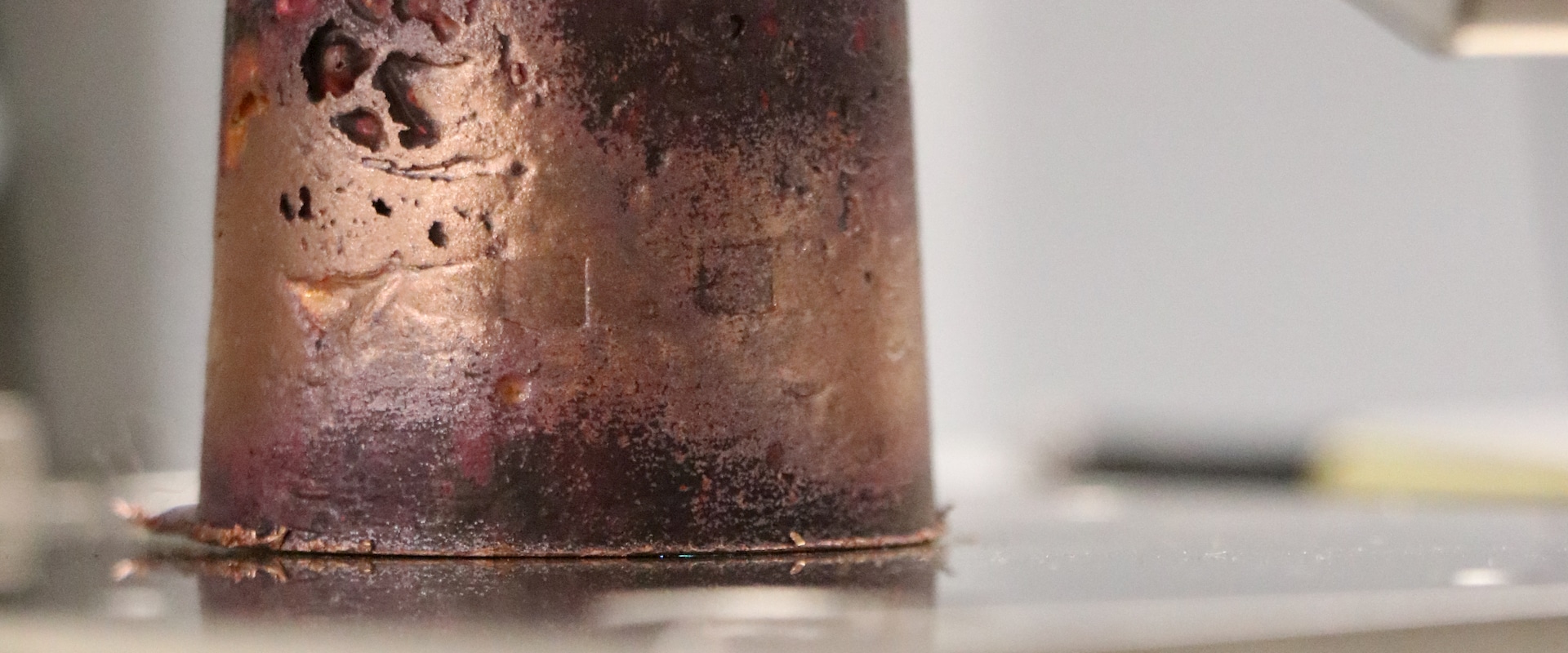
Manufacturing in the U.S. has had a long love affair with materials research for efficiency. Production ideologies like Lean Manufacturing have emerged to save Manufacturers time, money, and higher quality products.
The only problem?
Almost no one is taking advantage of their material waste.
Manufacturing Waste Management Is The Goal
Lean Manufacturing is the process of reducing waste in every step of the production cycle. Created by Toyota as the Toyota Production System, Lean Manufacturing seeks to drive down cost and perfect the product design to maximize profits.
Six Sigma and MVP, or Minimum Viable Product, follow this same train of thought. The goal for each of these is to create a manufacturing waste management system for your operation.
Scrap waste often gets brushed aside both figuratively and literally for safety and to increase production time. But what if you could get more out of it?
How You Gather and Dispose of Scrap Matters
Where swarf and chips can endanger the production line if left unchecked, the collection method can hurt your cost. When scrap waste is collected and packaged for recycling, it shaves off the additional time needed for pickup and sale to a metals recycler.
In an organizational strategy where the distance and travel time matters on the production line, the time vehicles are in your loading bay can hamper your delivery time. Loading-bay operations are even more critical for Direct To Consumer (DTC) Product Manufacturers.
When constantly competing with Amazon’s two-day shipping cycle, the time hauling that scrap for sale is critical to completing one of the base rules of Lean Manufacturing: improve the flow stream.
Remanufacturing Could Revolutionize Your Improvement Process
While the idea has been around for decades, few U.S. manufacturers have capitalized on the scrap remanufacturing process. When innovating to meet new market demands, you can use remanufacturing to reduce material costs.
This practice is already being perfected in the place you’d least expect it: fashion manufacturing.
Brands like Zara, Supreme, and H&M use remanufacturing to cut production costs at their knees and compete with new trends at lightning speeds.
Tackle Your Cost At Both Ends of Your Supply Chain
The biggest secret to these brands’ success is their Lean Manufacturing and supply chain management. To afford lighting-speed operation time outside of the production line, they leverage textiles recycling and remanufacturing.
Textile recyclers then take these leftover natural and synthetic cloth to produce new material, rags, and plastic wire covers. The brand then returns to the textile recycler to buy recycled fabric cheaper than they could anywhere else.
It’s Even Easier With Metals Recycling
Some manufacturers know that they can get cheaper metals, but are often worried about the quality that comes from recyclers, despite the metals being correctly graded. Others don’t want to waste time figuring out new ways to deal with their scrap waste.
Metals recycling has come a long way since the first arc reactor in the 1800s. The quality of recycled goods is now undeniably equal to newly mined metals. Steel is 100% recyclable, while we recycle ores like aluminum, copper, and titanium dozens of times before seeing quality loss.
Proven By Trade and Manufacturing Organizations
Enter the U.S. International Trade Commission (USITC) and REMADE, a manufacturing USA Institute, backed by the U.S. Department of Energy.
Without incorporating Lean Manufacturing or Six Sigma tactics, the USITC found that companies utilizing remanufacturing saw a whopping 50-90 percent of their original product material reused. So everyone must be using this process to save money, right?
They only found that 2 percent of the market’s total sales were using remanufacturing.
The Department of Energy Is Urging You To Innovate
REMADE was established to use new technology and techniques to secure the future of U.S. manufacturing industry. The organization is a public-private partnership looking to help manufacturers improve their design process to compete with the international industry.
The same country of innovators that revolutionized the industry by inventing the production line is at risk of losing the technological advantage we’ve had for years. To meet cost, you’ll need to secure your Manufacturing Waste Management.
You’re Not Alone
GLE Scrap Metal, a national metals recycler, in part with our sister company Great Lakes Electronics Corporation, a national Ewaste recycling company, have helped a multitude of companies secure logistics and transportation for their scrap metal and reduce production costs.
Companies that practice proper Lean Manufacturing and Remanufacturing practices are outperforming their markets everywhere. Together, we can be part of the solution and help you build a better product. If you’re ready to get started, contact us here, or give us a call at 855-727-2788.