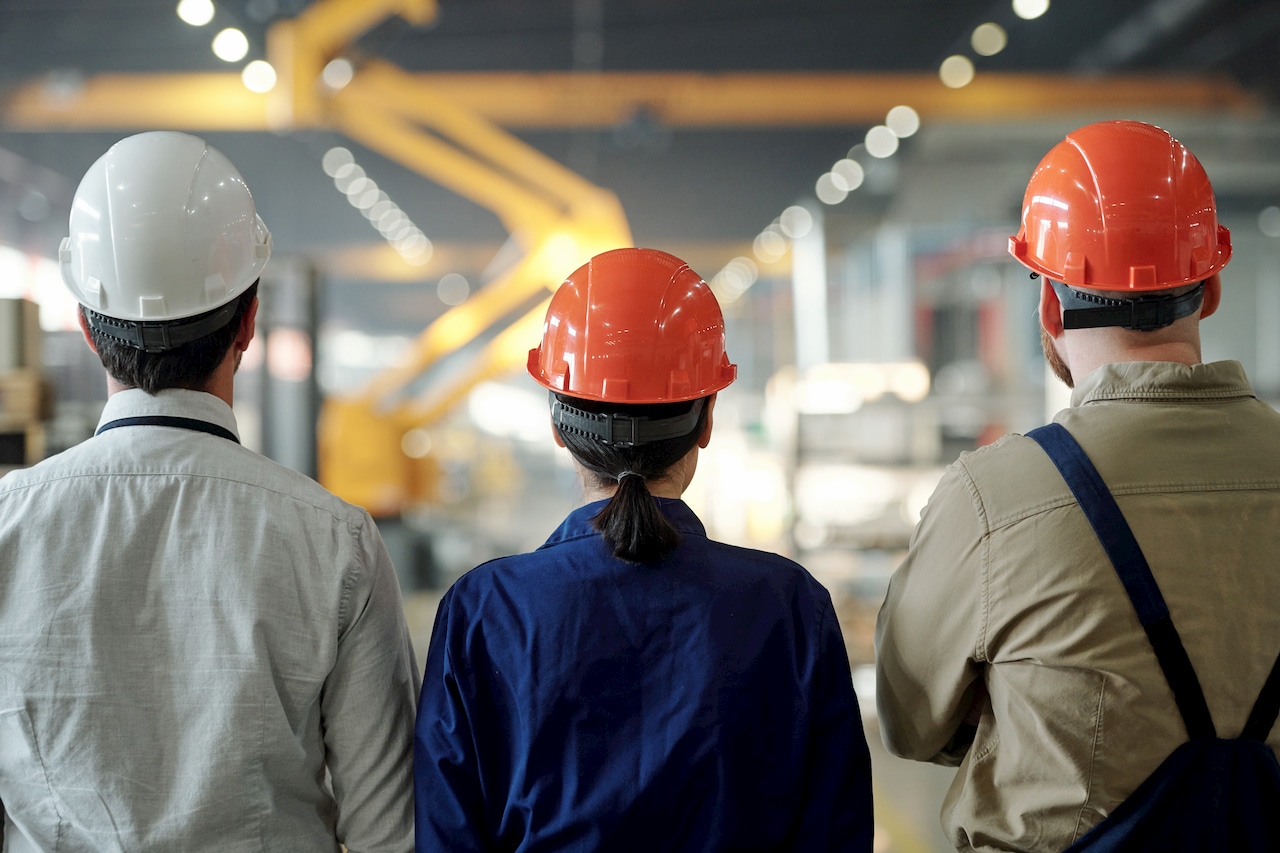
Will manufacturing return to the US?
It’s happening right now, but probably not the way you’d imagine it. Coronavirus has shaken the faith in the current business model most US Manufacturers use: Lean Manufacturing. Now manufacturing leaders are picking up some old tactics that are bringing jobs back to the US.
But what kind of jobs can we expect? Just what happened that a 70-year-old business model is finally changing?
Are Manufacturing Jobs Coming Back To The US?
In early February 2020, major US metal-based manufacturers such as John Deer, Morton Industries, and Caterpillar made the shocking jump to reinvest in US Manufacturing.
China’s manufacturing production came to a halt, and there was no sense of how long supplies would be on hold. These manufacturers and others like them scrambled to find new US suppliers.
But that’s not all that shifted in the global supply chain, and it doesn’t paint the right picture on where US manufacturing was before and after the shift.
Modern Manufacturing
Today, manufacturing isn’t as simple as it was during the time of the Model-T and the golden-era of US manufacturing. We can think of manufacturing as typically being broken down into five parts:
- Casting (or forging)
- Prefabrication (Typically known as prefab)
- Assembly
- Testing
- Packaging
These five steps tend to be scattered around the world, with China taking the lion’s share of the first two steps in the manufacturing process and manufacturing jobs. In contrast, US Manufacturing has recently been the assembly stage, finally with testing and packaging often ending somewhere else.
The Scramble For Tools and Equipment
The inability to source prefab materials left US Manufacturers with the need to hire local experts quickly. The only problem? Die shops, CNC machining, and other US prefab businesses are much smaller than their overseas counterparts. They either can’t handle the volume of business or quickly filled up on too many contracts.
Instead, larger manufacturers have made the jump to integrate the casting and prefabrication within the US to mitigate this supply-side damage in the future. That jump caused a mad scramble for tools and equipment created on the same supply lines that were stalling.
The squeeze on the market left a lot of smaller manufacturers with substantial shortages.
The Early Effect On Supply Lines
Without the ability to source raw metals and materials, manufacturers have had to start using older practices on stocking, retaining skill-based contractors, and radically changing product costs.
The lack of an epidemic, viral or otherwise hitting the US supply chain for over 70 years may be a significant contributing factor. For a long time, US Manufacturers could trust international suppliers to be reliable. There was no fear of war or significant illness causing a problem. US manufacturers could integrate further and further to drive down costs.
But now, manufacturers ran to bring back jobs to the US and closer countries and invest in the healthier US population. Then the pandemic came to the US.
US Manufacturing Hit On Both Sides
Most fast, efficient assembly lines require workers to stay close together along the line. That closeness is a known hazard for an extreme disease but typically isn’t an issue. But as Covid-19 began to infect workers, it started to cause more problems than it solved.
As NPR reported back in August 2020, Honda and other major manufacturers have been forcing white-collar workers to fill in for sick assembly line workers as they run out of healthy employees.
Contract Manufacturers Mark The Second Major Change
Come August, many of the manufacturers finally started to have enough US staff to stop shortages, however they now faced a new problem: they didn’t have enough workers.
New equipment and tools won’t go to waste in future years; manufacturers have learned the hard way they need to diversify their workforce and supply lines.
US manufacturers now had to go back to contract manufacturers internationally, but still couldn’t use their connections with Chinese suppliers for risk of exposure to the virus. These businesses began to create new contracts with businesses in neighboring countries to drive down the delivery time. Then, they moved to start using more recycled metals from US recycling companies.
What This Means For US Manufacturing So Far
We can see three significant changes the savviest manufacturers have taken that will most likely shape the future of US Manufacturing:
- New contracts and contractors now span the US and businesses outside of China
- Manufacturers have had to rapidly develop a local supply chain before assembly with new tools and equipment
- Many are now using more recycled metal to avoid the high steel and aluminum tariffs to recover costs
While we’re likely to see a shift back to Chinese manufacturers once these new contracts end, don’t expect the latest tools, equipment, and contractors to go away anytime soon. With such a fundamental shift in procuring resources, there will be more manufacturers shifting to this safer, less optimized model. Which should mean more US Manufacturing jobs in the future.
China’s Electric Wholesalers
But for China’s electric wholesalers, there’s a different problem. Generally unknown to most Americans, Shenzhen, is the powerhouse city most responsible for China’s electronics industry.
Chip and board manufacturing is almost non-existent in the US, and we don’t currently have the machines to maintain that type of factory here. We do efficiently recycle those electronics, but US electronic manufacturing still isn’t ready to fix that supply problem.
How It’s Shifting Air Freight
Typically, Air Freight has been more of a focus for finished shipping products, whereas manufacturers usually use Ocean Freight for material supplies and shipping. As long as supplies are un-interrupted, the process runs smoothly.
In desperation to prevent shortages, many manufacturers have had to use Air Freight from their Chinese suppliers. But since Air Freight was also suffering from Covid-19, prices reached their peak in May due to surcharges from excessive demand.
Since the break-up between FedEx and Amazon, following the significant blow to the freight industry, we’re likely to see manufacturers find shorter routes for their supplies. With manufacturers already invested in local equipment and workers, it’ll be easier to save in transportation costs.
The Over-Optimized Supply Chain
US manufacturing got the brunt of this problem from following the Lean Manufacturing business model. The practice is a highly effective cost-cutting strategy that generally works wonders. Unfortunately, a pandemic targets the specific weaknesses this strategy suffers.
Demand-based Inventory
To reduce warehousing costs, Lean Manufacturing preaches that you should only procure resources based on incoming orders. That dramatically reduces the cost of materials but can create shortages when the supply managers can’t adapt fast enough.
Tiny Work Environments
To increase worker productivity without increasing their workload, Lean Manufacturing offers to keep all equipment as close to the worker’s station as possible, to reduce trip time. This smaller work environment doubles as a sanitization hazard, but only under the extreme conditions of a pandemic.
Minimum Viable Product
If you want to follow this same form of manufacturing, you also need to go with the cheapest, reliable supplier. Chinese manufacturers have made that a national and industry-standard. That leaves most US manufacturers with nowhere to cut their budget if those suppliers fall through.
Bringing Back Redundancies
The truth is, the global manufacturing supply chain has been historically extremely stable since World War Two. The lack of significant illness or ground wars has led to a highly integrated chain for both the US and China. However, since redundancies haven’t had a major cost benefit for over a generation, many businesses just stopped including them.
With all these things benefiting Manufacturing in the US, will we really see jobs return? We’ll need to empower US Suppliers.
Feeding and Securing US Suppliers
As the surviving manufacturing companies come out the other side with scrapes and bruises, we’re likely to see a rise in more affordable US scrap metal being used and prefabricated in the US rather than overseas. It still won’t be like it was before the US shifted large parts of the manufacturing process internationally.
Instead, US manufacturing jobs will likely see an increase from businesses more willing to keep smaller shops and factories open in the US, with the ability to scale up if there’s a similar shake-up in the near future.
Find The Right Manufacturing Recycler
Now more than ever it’s important to recycle scrap. Looking for a scrap facility to process your recycling? It’s essential to establish a relationship with a scrap processing specialist that you can trust. They’ll help you get your scrap recycling to the right facilities.
When you bring your scrap into the right centers, they can process the materials on-site, netting you more for your scrap.
GLE Scrap Metal
GLE Scrap Metal can help you as a national recycling company, with locations across the eastern US. Not only can they help local states, but they can also help arrange your scrap to be shipped to the right facilities across the US, so you get the most from your efforts. Give them a call at 855-727-2788 or contact them here.